The difference between single screw extruder and twin screw extruder
Taking the production of aquatic feed as an example, the advantages of twin-screw extruder lie in:
1. Material adaptability is wider. It can be used for processing materials with high viscosity, low viscosity, high oil content, high moisture or viscous, oil-rich, very wet and other materials that will slip in a single screw.
2. It has less restriction on the size of raw materials, and can be adapted to the processing of raw materials from micro-powder to coarse powder and materials with particle size beyond the specific range of single screw processing.
3. Material flow is more uniform in the barrel. Steam and water can be added to make the product meet the demand.
4. The internal and external quality of the product is better. It can achieve a very good homogeneous state and make the molecular structure of the material uniformly arranged. The surface of the product is smooth during the extrusion process. The product has high uniformity and uniformity.
5. The ripening homogeneity effect is better, usually the starch ripening degree can reach more than 95%, which makes the processed aquatic feed stable in water and the nutrients of the product are not lost, and easy to digest and absorb.
6. The output is higher under the same power. Good mixing performance makes the heat of material uniform in time, accelerates the maturation degree of material, reduces the fluctuation of material temperature, and improves the output of extruded products.
7. Product diversity and adaptability are wider. It can process particulate aquatic feed, high oil formula, high moisture, high viscous products and products with multi-color, sandwich and special shape.
8. The process operation is simpler, and the spindle speed can be adjusted according to the requirements of the processed products. Because of the self-cleaning characteristics, cleaning is very convenient, and there is no need to disassemble and assemble equipment after each processing.
9. Wear of vulnerable parts is lighter. A common misconception is that the wear of single screw is less. In fact, due to the stable material transportation and material flow during twin screw extrusion, the wear of material on screw and inner sleeve of barrel is smaller than that of single screw. Although the number of screw is more than one set, the cost of accessories is still lower than that of single screw.
10. The cost of production is lower. Because the twin-screw machine has good operation stability, it has fewer waste materials, less waste of water and gas, less man-hour, high heat transfer efficiency, high rate of finished products, high power output index, and low cost of accessories, its final production cost is much lower than that of single screw.
компанія:
адреса:
телефон :
Електронна пошта :
Skype :
Whatapp/Wechat:
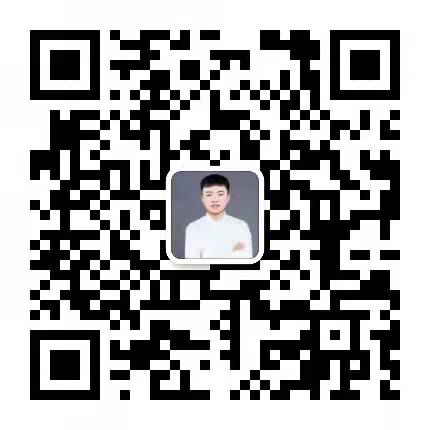